Warning to Offshore Companies from HSE
The UK's HSE has issued a new safety alert to offshore companies
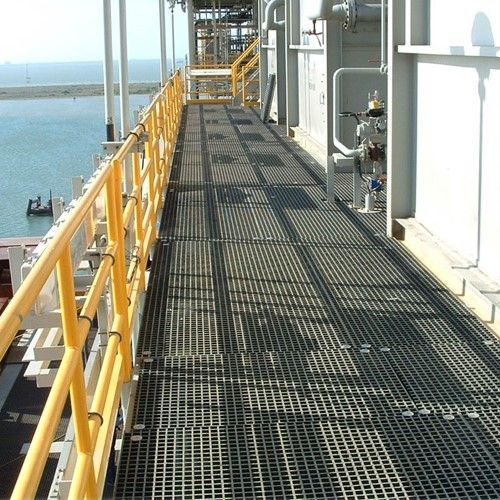
HSE has issued a safety alert about the unsafe use of floor grating systems on offshore oil and gas platforms, vessels and wind generation installations.
Sections of polymer floor grating systems can become dislodged, with workers and others at risk of tripping on unsecured flooring or falling through the subsequent hole.
Recent Investigations have revealed that fasteners used to secure the polymer grating flooring sections, often called GRP have not been installed or positioned as per the original equipment manufacturer’s (OEM) guidance, or in line with industry good practice.
Duty holders, owners, operators and employers should identify all areas of grating systems across installations and workplaces, and carry out a suitable and sufficient review to ensure they are safe to use and fit for purpose.
Safety critical areas such as escape routes should be prioritised with immediate effect.
Offshore Grating Issue
Sections of polymer floor grating systems, used on offshore oil and gas platforms, vessels and wind generation installations, can become dislodged. Workers and others are at risk of tripping on unsecured flooring or falling through the subsequent hole.
Grating-systems (used on walkways and deck areas) on offshore installations can be damaged or dislodged during rig moving operations. People may be harmed if walkways and emergency access and egress routes are damaged during rig moves. The risk of damage to these systems may increase during adverse weather or sea state.
Outline of the problem
Investigations have revealed that fasteners used to secure the polymer grating flooring sections have not been installed or positioned as per the original equipment manufacturer’s (OEM’s) guidance, or in line with industry good practice.
HSE is aware of incidents of damaged and dislodged gratings that have presented risks of harm to personnel on offshore installations operating on and outside of the United Kingdom Continental Shelf (UKCS). The grating-systems can be damaged by adverse weather conditions such as wave impact. Damage can occur when moving rigs including towing, moving semi-submersibles, jacking, or manoeuvring jack-up rigs. The condition of grating systems may also deteriorate over time.
Action required
Duty holders (including Operators and owners of offshore installations) should carry out a risk assessment of the types of grating system used on their installation, and the potential for it to be dislodged or damaged during rig moving operations, by adverse weather and sea state.
Once you identify any hazards, you should eliminate or control the risks, so far as is reasonably practicable.
Assess risks for all modes of operation
Operational hazards and risk profiles are likely to change when an installation enters a different mode of operation. Duty holders should assess risks regarding any grating systems to ensure their reliability and safe use during those differing operational activities. For example, in rig moving mode it is not uncommon for deck areas and walkways to be closer to the water surface.
A change in weather or sea state may require the temporary (or permanent) closure or restriction of access to specified areas, doorways and/or walkways, and the consideration of revised muster points and escape routes.
Design, installation and maintenance
Consider the suitability and design of your grating systems to determine areas where the installation may be more susceptible to damage during different modes of operation (such as jacking and/or wet tow activities).
Ensure all grating systems are subject to regular inspection and maintenance to check that they are installed correctly and as per any manufacturers guidance and remain in effective working order.
Employees or contractors that design, install, inspect and/or repair grating systems should be sufficiently competent to undertake their role.
Operational policies and procedures
Operational policies and procedures, such as your adverse weather policy, should consider what actions may be necessary if weather conditions or sea state change and impact on the safe undertaking on any activity.
Your operational policies and procedures should adequately consider the risks associated with rig moves as well as risks during jacked up or moored operations. And if necessary, work activities during moving operations should be temporarily or permanently modified and/or restricted to ensure the safety of personnel.
You should consider if a system for accounting for the whereabouts of all persons working outside of the accommodation areas would provide further control measures to rig moving activities.
It is not uncommon for individual workers to work extended hours during rig move operations and to have more than one operational role for different phases of operation. You must adequately assess the increased risk of fatigue and control it. Ensure that there is either sufficient rest and/or adequate cover for safety critical roles and responsibilities.
Emergency response arrangements
In the event of a missing person or person overboard, those involved in rig move operations must ensure that effective emergency response arrangements are in place. This should include, but not necessarily be limited to, how an installation will respond and what actions must be taken to report missing person(s) or person(s) overboard.
When undertaking a rig move risk assessment your Emergency Response Plan (ERP) should adequately consider (but not necessarily be limited to):
- the possibility of a person falling overboard when in transit
- the suitability of rescue and recovery equipment, and crew competence in using that equipment
- the ability of installation personnel to launch a rescue boat and recover a person(s) in a timely fashion - it may be more appropriate to assign responsibility for rescue and recovery to others (such as one of the towing vessels if it is equipped for such operations)
- training and testing of ERPs is in place to assure effective communications with the Coastguard during the different phases of response (commonly referred to as the Uncertainty Phase, Alert Phase and Distress Phase)
- your ERPs are aligned with accepted industry standards, such as the International Aeronautical Maritime Search and Rescue (IAMSAR) manual
- suitable communications systems are available and tested so that they can be relied upon in a dynamic marine environment, and what actions to take if a system is impaired or unavailable.
Identify where grating systems are used
Duty holders and employers should identify all areas of grating systems across installations and workplaces.
Prioritise safety critical areas
Prioritise safety critical areas such as escape routes and carry out a suitable and sufficient review to ensure they are safe to use. This should include but not be limited to ensuring they are installed in accordance with the original equipment manufacturers (OEM) instructions for the use of fasteners.
Offshore Grating Application
How did polymer flooring come about in the application of the offshore industry and subsequently offshore wind?
Glass Reinforced Plastics (GRP) and Fibre Reinforced Plastics (FRP) are typically the same thing and manufactures offer a range of products suitable for oil rigs, wind farms and other offshore applications. Some are DNV & ISO approved, and have been impact tested for dropped object protection for the seabed. Including manufactures of offshore gratings offering a range of fire retardant resins that are ideal for creating access solutions with wind turbines.
Typical GRP System Benefits:
- Resistant to rot and mould
- Extremely hard wearing and durable
- Corrosion resistant
- Lightweight
- Easy to handle and install
- Low maintenance cost when installed correctly
Fibre Reinforced Plastic (FRP) grating for the offshore industry
The use of Fibre Reinforced Plastic grating has many advantages in comparison with the much-used steel grating, particularly for the offshore industry. Fibreglass Reinforced Plastic grating is high in strength and corrosion-resistant, is lightweight, has a long service life and is safe in use: nonskid and excellent anti-slip properties.
Fire safety of Fibreglass Reinforced Plastic grating
With regard to the specific fire safety requirements in the offshore sector, pultruded grating is regularly used in the offshore and oil and gas industries.
Why Fibreglass Reinforced Plastic grating is used in the offshore industry?
- chemical resistance: Fibreglass Reinforced Plastic grating is highly resistant to corrosive substances and acids
- lighter than steel: Fibre Reinforced Plastic (FRP) grating is a third to a half the weight of steel grating
- impact-resistant: FRP grating is more impact-resistant than steel grating
- nonskid and anti-slip properties: the concave meniscus surface makes the FRP grating extremely nonskid and it has very positive anti-slip properties
- maintenance-friendly: FRP does not rust and does not rot: low maintenance
- optional antistatic top surface
- electrically and thermally non-conductive
- easy to process and install
Why HSE Issued the Safety Alert?
The HSE has issued a warning to all oil and gas and offshore wind operators to check over their vessels amid fears a worker went through a hole in the floor of a North Sea rig. 50-year-old Jason Thomas has not been recovered since going missing from the Valaris 121, 100 miles off Aberdeen, in January. A Health and Safety Executive (HSE) notice, published last week, confirmed fears that he went through a hole in the rig decking – which was discovered on January 22; the same day he went missing.
The notice stated a section of polymer grating had been dislodged putting employees at risk of “falling through the subsequent hole”.
A new safety alert from the watchdog states that sections of polymer floor gratings, used on offshore oil and gas platforms, vessels and wind generation installations, can become dislodged. The alert calls for all duty holders and employers to identify all areas of grating across their installations to ensure they are safe, prioritising safety-critical areas.
“Workers and others are at risk of tripping on unsecured flooring or falling through the subsequent hole.”
It adds: “Investigations have revealed that fasteners used to secure the polymer grating flooring sections have not been installed or positioned as per the original equipment manufacturer’s (OEM’s) guidance, or in line with industry good practice”.
On the HSE notice published last week, RMT Union boss Jake Molloy said that it “confirm(ed) that our fears were fully verified” that Mr Thomas may have gone through the grating hole.
Last week the HSE said it is continuing to investigate the circumstances and is liaising with authorities.
It added: “No further detail will be given during the investigation. We have been in contact with Jason’s family, with whom our thoughts remain.”
About Dangle Rope Access
Here at Dangle Rope Access, we provide a variety of comprehensive inspection, access, coatings, and composite (IACC) industrial services. Our services are available to both the private and public sectors.
We offer high-quality proven solutions that will help reduce maintenance costs in both the long and short-term. We are based in Dundee, Scotland and also have offices based in Edinburgh, along with our newly established training centre in Northern Ireland Dangle Academy. Due to our company size and structure, we are able to offer a flexible and versatile approach to the way we run our business and the services that we offer our clients. And, as a leading painting company, we’ve worked on several renewable energy projects in the UK, Europe, and the US.
We work with both on and offshore with wind farm operators, and asset owners. For offshore wind farm maintenance, to onshore building maintenance, we can cover both the East and West coasts.
To find out more about how our team can help you contact us today. Our friendly, professional and helpful team is always on hand to help.