Protective Coatings
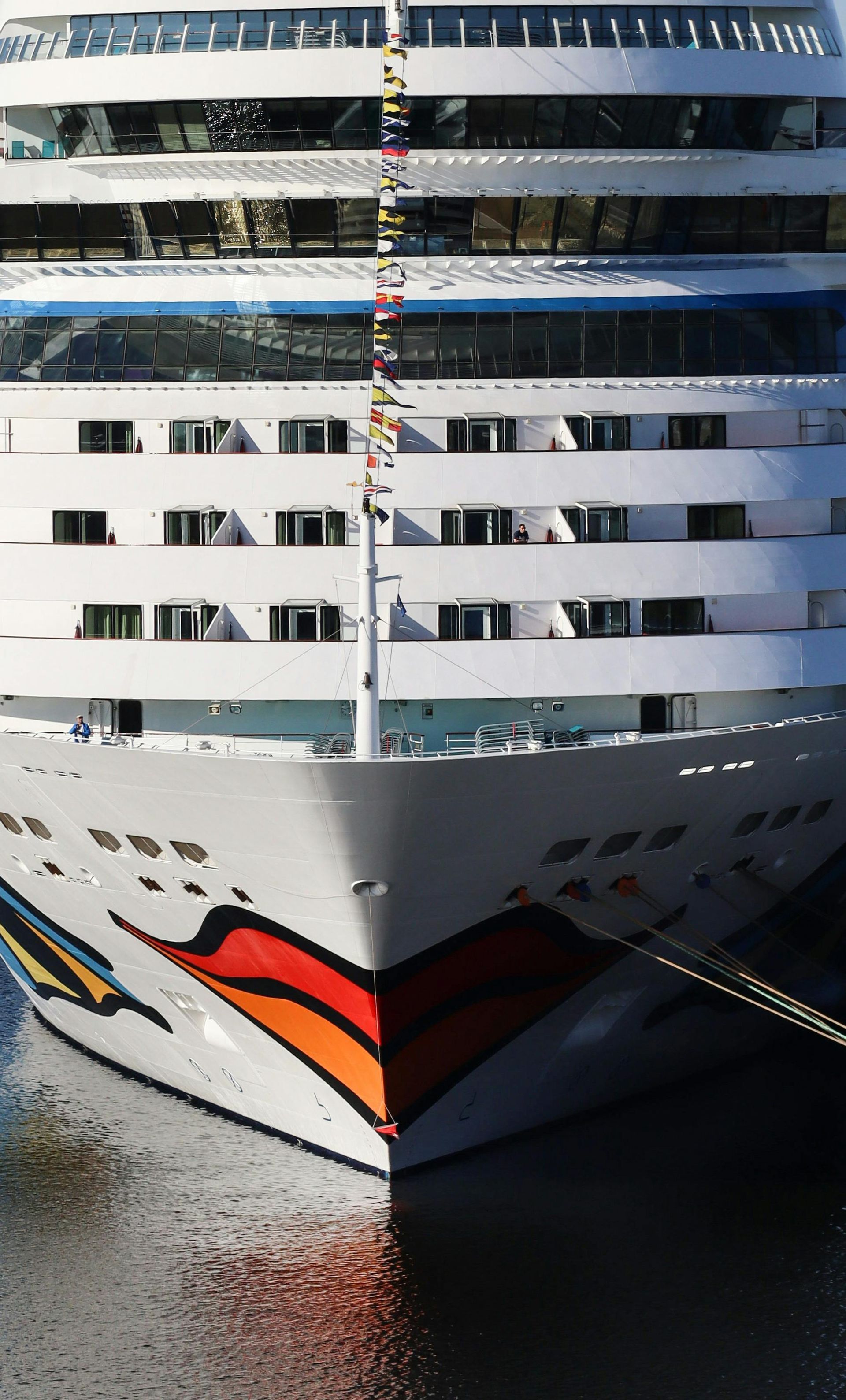
The Science Behind Protective Coatings
Protective coatings play a crucial role in safeguarding industrial structures, machinery, and infrastructure from corrosion, weathering, chemicals and mechanical wear. These coatings are more than just paint—they are engineered to provide long-term durability, efficiency and resistance to harsh environmental conditions.
However, choosing the right protective coating is not as simple as picking a colour or brand. The science behind coatings involves understanding material properties, environmental exposure and application techniques. Selecting the wrong coating can lead to premature failures, costly repairs, and even safety risks.
In this guide, we will explore the science behind protective coatings, the different types available, how to choose the right one, and why hiring a specialist like Dangle is critical for ensuring long-term success in coating projects.
What Are Protective Coatings?
Protective coatings are specialised paints designed to extend the lifespan of structures and equipment by forming a semi-permeable barrier against damaging elements in the environment in which they are placed. Unlike standard decorative water based paints, these industrial coatings prioritise functionality and safety, offering corrosion resistance, chemical protection, UV stability, and mechanical durability.
Industries such as construction, oil and gas, marine, renewables and manufacturing rely on protective coatings to maintain the integrity of critical assets, including bridges, offshore platforms, windfarms, pipelines and heavy machinery.
How Do Protective Coatings Work?
The effectiveness of a protective coating depends on several key factors:
• Adhesion – How well the coating bonds to the substrate.
• Cohesion - How well the coating bonds to the paint underneath in a multi coat system.
• Permeability – Resistance to water and air penetration.
• Chemical Resistance – Ability to withstand exposure to aggressive chemicals.
• Mechanical Durability – Resistance to impact, abrasion and physical stress.
• Ultra-Violet Resistance - Resistance to exposure from sunlight (UV rays) over time.
Modern coatings often incorporate advanced additives, such as corrosion inhibitors, UV stabilisers and fire-retardant compounds, to enhance performance and extend the life of industrial assets.
Types of Protective Coatings
Different coatings offer varying levels of protection, and selecting the right one depends on environmental conditions and material compatibility.
Epoxy Coatings
Best for: Industrial flooring, pipelines, steel structures, chemical plants.
Why? Epoxies provide excellent adhesion, chemical resistance, and durability.
Strong adhesion to metal and concrete.
Resistant to chemicals, solvents, and moisture.
Smooth matt layer.
Polyurethane Coatings
Best for: Outdoor structures, marine environments, high-traffic areas.
Why? Polyurethanes offer superior UV resistance and flexibility.
Weather-resistant and UV-stable.
Good abrasion and chemical resistance.
Remains flexible, preventing cracking.
Zinc-Rich Coatings
Best for: Steel bridges, offshore platforms, pipelines.
Why? These coatings provide sacrificial anodic corrosion protection.
Excellent long-term rust prevention.
Ideal for highly corrosive environments.
Usually requires very thorough surface preparation.
Acrylic Coatings
Best for: Commercial buildings, light industrial applications.
Why? Acrylic coatings are fast-drying and cost-effective.
Lower VOC (volatile organic compounds) missions than typical Epoxy or Polyurathane paints making them more environmentally friendly.
Quick drying and easy to apply.
Intumescent Coatings
Best for: Fireproofing steel structures in buildings and industrial facilities.
Why? These coatings expand when exposed to fire, creating an insulating barrier.
Essential for fire safety in structural applications.
Compatible with various surfaces.
Requires precise application to maintain effectiveness.
May need additional weather-resistant topcoats.
Water Based Coatings
Best for: Durability and environmental safety
Why? These coatings are quick-drying, low in volatile organic compounds (VOCs).
Low VOC emissions and environmentally friendly.
Quick drying and easy to apply.
Technology advances in paint manufacture mean higher volume solids (V/S).
How to Choose the Right Protective Coating
Selecting the best protective coating involves several considerations. For more detailed information on how much paint your project may need please see our other blog post on Coating Calculations.
Environmental Factors
• Marine environments – Require coatings with an ability to withstand saltwater and moisture.
• Chemical exposure – Industrial settings need coatings resistant to acids, solvents, and oils.
• UV exposure – Outdoor structures should have UV-resistant coatings like polyurethanes.
Surface Material
• Steel – Needs anti-corrosion coatings such as zinc-rich primers or epoxies.
• Concrete – Requires coatings that resist water penetration and chemical attack.
• Wood – Must be protected from moisture, UV exposure, and decay.
Application Methods
• Brush and roller – Suitable for small areas or detailed work.
• Spray application – Best for large, complex surfaces requiring uniform coverage.
• Dipping and immersion – Ideal for coating components needing full coverage.
Longevity and Maintenance
• Long-term protection – Epoxies and zinc-rich coatings offer extended durability.
• Ease of maintenance – If frequent re-coating is needed, the coating should allow easy reapplication with long overcoating intervals for chemical cohesion.
Overcoating Intervals & Curing Times
• Extended Overcoating – Allows over coating with fresh paint for longer durations for cohesion.
•
Drying Times – The longer the curing time of the paint usually means the longer the item thats been painted is out of service.
Surface Preparation Prior to Application of Protective Coatings
Even the most advanced protective coating will fail if the surface is not properly prepared. ISO 12944 is the international standard for corrosion protection of steel structures by protective paint systems and this document describes the types of paint and paint system commonly used for corrosion protection of steel structures.
It also gives guidelines for the selection of paint systems available for different environments (see ISO 12944‑2) and different surface preparation grades (see ISO 12944‑4), and the durability grade to be expected (see ISO 12944‑1).
.
Common Surface Preparation Methods:
Abrasive Blasting (media blasting): Removes rust, old coatings, and contaminants.
Power Washing: Cleans dirt and grease, and loosely adhering old coatings before painting.
Chemical Cleaning: Removes oil and residues that could affect adhesion.
Pickling or Etching: Pickling and etching are metal surface treatments using acids to enhance adhesion.
Neglecting surface preparation can lead to premature coating breakdown such as peeling, blistering, and increased maintenance costs.
Choosing a Coating Specialist for Protective Coatings
While selecting the right protective coating is crucial, the success of any coating project also depends on proper application. This is where the expertise of a coating specialist becomes invaluable and Dangle are expert coating contractors.
Why Hire a Coating Specialist?
Technical Knowledge: Specialists understand the chemistry behind coatings, ensuring compatibility with different materials and environments.
Correct Surface Preparation: Professionals use industry best practices to prepare surfaces properly, maximising adhesion and durability.
Application Expertise: A specialist in the field, like Dangle ensures coatings are applied under the right conditions, with the correct thickness and drying times.
Safety Compliance: Industrial coating projects often involve working at heights, handling hazardous materials, and complying with strict safety regulations. Specialists ensure work is done safely and in accordance with industry standards.
Long-Term Cost Savings: Poorly applied coatings can lead to costly rework and premature failures. Investing in a specialist reduces these risks and extends the life of the coating.
What to Look for in a Coating Specialist
• Certifications: Look for contractors with industry-recognised certifications, such as those from ICorr (Institute of Corrosion) or NACE (National Association of Corrosion Engineers now AMPP).
• Experience: Choose a company with a proven track record in your industry.
• Customer Reviews: Check testimonials and case studies to ensure quality workmanship.
• Warranty and Support: Reliable specialists offer guarantees on their work and ongoing maintenance support.
By working with an experienced coating specialist, you can ensure that your investment in protective coatings delivers long-lasting performance and value.
Learn More About Dangle Rope Access Today
Here at
Dangle, we provide a variety of comprehensive inspection, access, coatings, and composite (IACC) industrial services. Our services are available to both the private and public sectors.
We offer high-quality proven solutions that will help reduce maintenance costs in both the long and short-term. We are based in Dundee, Scotland and also have offices based in Edinburgh, along with our newly established training centre in Northern Ireland Dangle Academy. Due to our company size and structure, we are able to offer a flexible and versatile approach to the way we run our business and the services that we offer our clients. And, as a leading painting company, we’ve worked on several renewable energy projects in the UK, Europe, and the US.
We work with both on and offshore with wind farm operators, and asset owners. For offshore wind farm maintenance, to onshore building maintenance, we can cover both the East and West coasts.
To find out more about how our team can help you contact us today. Our friendly, professional and helpful team is always on hand to help!
We'd love a share...
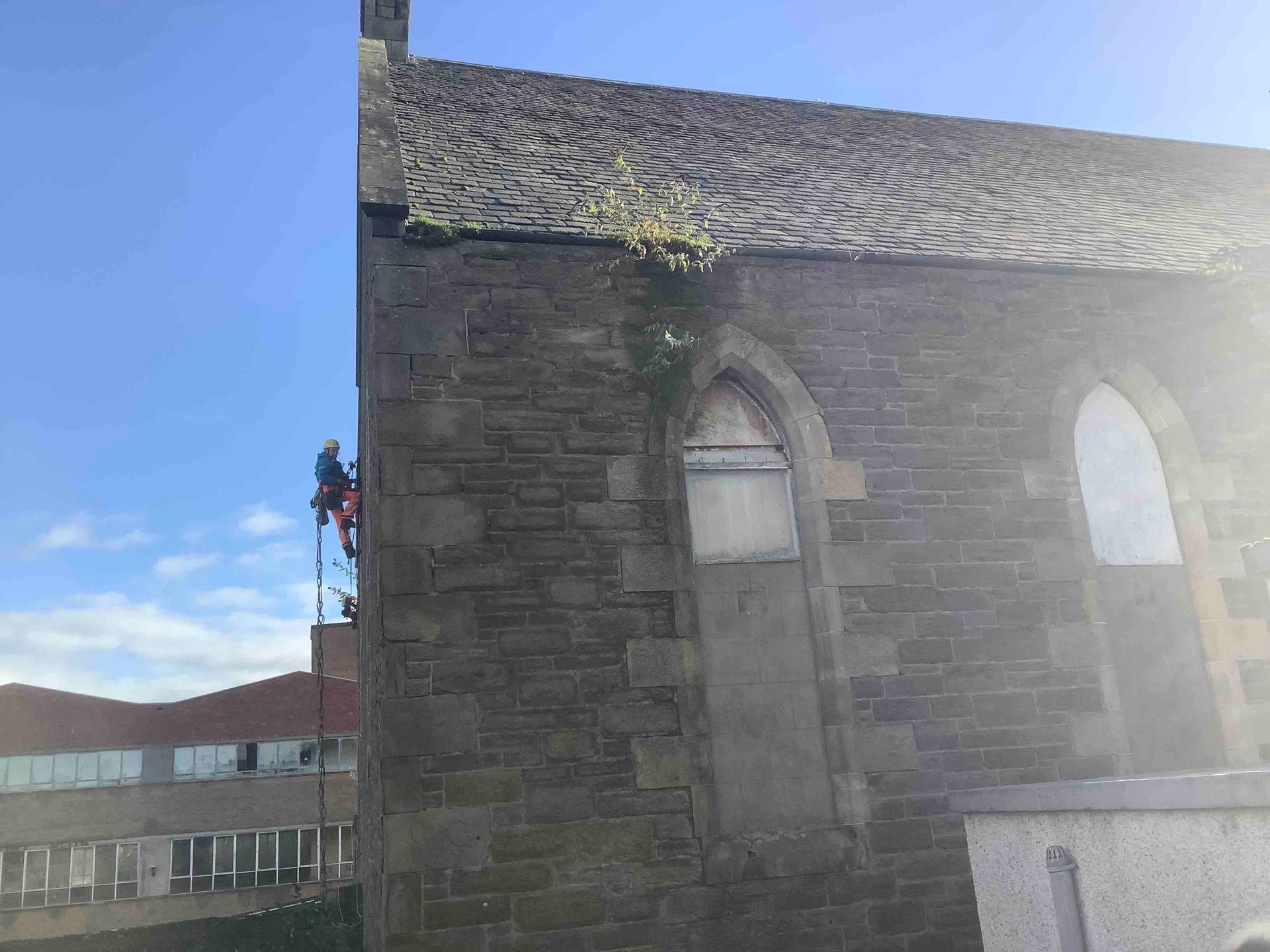