Zinc Rich Paints
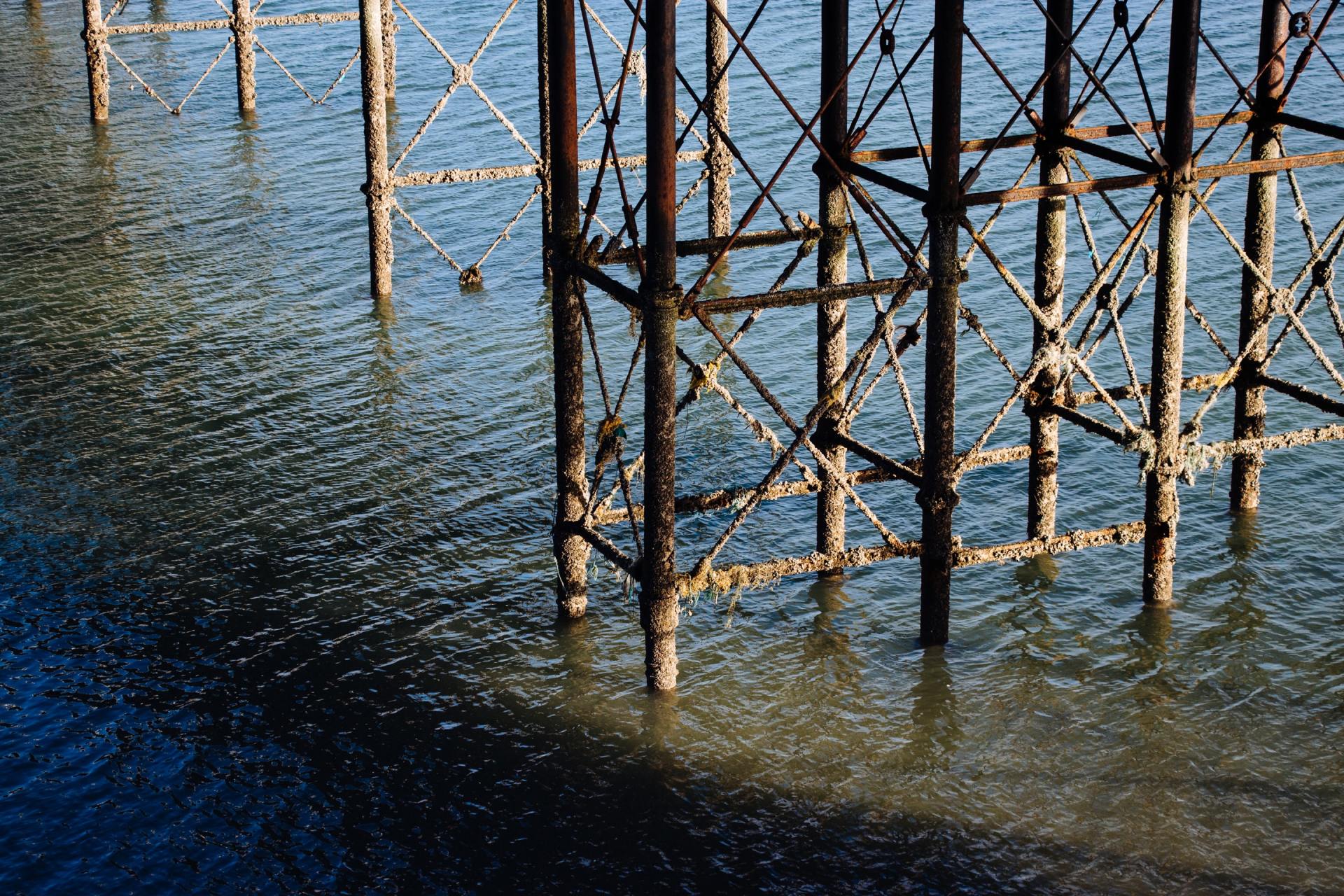
Zinc Rich Paints
Corrosion Control
The corrosion control behaviour of carbon steel coated with a zinc‐rich paint containingtwo metallic compounds, Al2(SO4)3 and CaO, as anticorrosive additives wasexamined recently, under wet and dry cyclic corrosion test conditions. The zinc‐richpaint coating without the two metallic compounds formed a white corrosionproduct (often referred to as zinc salts) and red iron rust on the surface after the corrosion test, whereas thecoating with the metallic compounds showed reduced surface corrosion products.
Interestingly, the corrosion current density of the painted steel substrate decreaseddrastically due to the incorporation of metallic compounds in the paint. Thezinc‐rich paint coating modified with the metallic compounds contained dispersed (Zn5(OH)8Cl2·H2O) phase and possibly very fine CaSO4particles, which remarkably improved the protectiveness of the zinc‐rich paintcoating, improving cathodic protection.
So what does all this mean? Well, steel is often employed as a structural material in infrastructures.However, the steel used in construction corrodes through reactions with corrosive agents in the environment in which it is placed, such asoxygen and water, under wet and dry cycles. Therefore, effective countermeasures arerequired to prevent atmospheric corrosion for maintainingthe steel infrastructures.
Several approaches have been proposed and appliedto prevent the corrosion of steel, including the applicationof protective coatings, the inclusion of corrosioninhibitors, and galvanic protection. Among them, a paintcoating is the most frequently used protective measurebecause of its versatility. In particular, zinc-richpaints are widely used to protect steel infrastructuresbecause of their high anticorrosive properties.
The maincomponent of a zinc‐rich paint is metallic zinc powder,which is considered to have anticorrosive propertiesowing to its sacrificial effect as well as the protectiveeffect of its corrosion products.In general, the anticorrosive properties of conventionalpaint coatings consisting mainly of a resin are attributed tothe barrier effect of the continuous resin‐rich film, whichprovides a semi-permeable layer or layers to the penetration of atmospheric corrosives to theunderlying steel substrate.
On the other hand, the zinc‐richpaint coating exhibits a lower barrier effect because of thelower resin fraction in the film. The main role of the resinin the zinc‐rich paint coating is to bind the metallic zincpowder particles in the coating, and the coated film inevitablycontains many defects owing to the lower fractionof the resin. Consequently, corrosives from the surroundingenvironment can more easily penetrate the zinc‐rich paint coating,and then the corrosion of metallic zinc powder particlesresults in the generation of alternative paths forcorrosives.
Moreover, further corrosion of the metalliczinc particles leads to a decrease in their sacrificial anticorrosiveeffect after the initial stage of corrosion. Therefore,to improve the anticorrosive effect of the zinc‐richpaint coating, it is indispensable to increase the protectiveeffect of the corrosion products of Zn.Effects of alloying elements to metallic zinc coating forsteel protection have been intensively investigated over a number of years. For example,the addition of metallic Al to hot‐dipped galvanisedcoating improved the corrosion protection performance ofthe coating. It has been reported in a Japanese study that alloying Al tozinc‐based metallic coating stabilised the corrosion productsof Zn. As for the zinc‐rich paint coating, it was also pointedout that metallic Al added to the coating improved thebarrier effect accompanied by the formation of Al oxide.
These imply that Al3+ eluted from the coatings modified thecorrosion products of Zn, resulting in the improved protectionof the coatings against corrosion. On the other hand, ionspecies other than Al3+ can also modify the corrosion resistanceof Zn. The same study examined passivating productsof Zn in a Ca(OH)2 solution and found that Ca2+progressed the growth of Ca[Zn(OH)3]2·2H2O (calcium hydroxyzincate)that passivated Zn surface. In addition, it wasreported that SO42− in marine droplets decreased the corrosionrate of Zn due to the formation of NaZn4Cl(OH)6-SO4·6H2O.
For rust grown on steels, it has beenreported that the supply of nonferrous metallic ions to therusts resulted in the modification of their structure, leadingto improvements in the protectiveness of the rusts. Furthermore, it has been reported that the supply of metalliccations to a steel surface in the early stage of the corrosionprocess resulted in the accelerated formation of theprotective rust layer. These reports imply that the presence ofion species such as Al3+, Ca2+, and SO42− in zinc‐rich paintcoating from the early stage of corrosion can quickly improvethe protective performance of the coating. To achieve a favourablesituation in a zinc‐rich paint coating, water‐solublemetallic compounds are focused.
Recently, it was demonstrated that water‐solublemetallic compounds added to an epoxy‐based paint providedmetallic cations in the paint during the corrosionprocess, improving the corrosion resistance of the paint-coatedsteel substrate by modifying the rust structure itself. Based on the aforementioned, water‐solublemetallic compounds added to a zinc‐rich paint could modifythe corrosion products of Zn, and thus improve the results of a protective effect of the zinc‐rich paint coating. In the study, the structure and protectiveness of the corrosionproducts formed in zinc‐rich paint coatings containingmetallic compounds on carbon steel were examined.
Why Choose Dangle?
Dangle is an award winning rope access company specialising in industrial coatings. We can help you to optimise your assets, operational and maintenance costs, with the latest developments in corrosion protection.
About Dangle Rope Access
Here at Dangle Rope Access, we provide a variety of comprehensive inspection, access, coatings, and composite (IACC) industrial services. Our services are available to both the private and public sectors.
We offer high-quality proven solutions that will help reduce maintenance costs in both the long and short-term. We are based in Dundee, Scotland and also have offices based in Edinburgh, along with our newly established training centre in Northern Ireland Dangle Academy. Due to our company size and structure, we are able to offer a flexible and versatile approach to the way we run our business and the services that we offer our clients. And, as a leading painting company, we’ve worked on several renewable energy projects in the UK, Europe, and the US.
We work with both on and offshore with wind farm operators, and asset owners. For offshore wind farm maintenance, to onshore building maintenance, we can cover both the East and West coasts.
To find out more about how our team can help you contact us today. Our friendly, professional and helpful team is always on hand to help.
Cathodic Protection
Corrosion Resistance
We'd love a share...
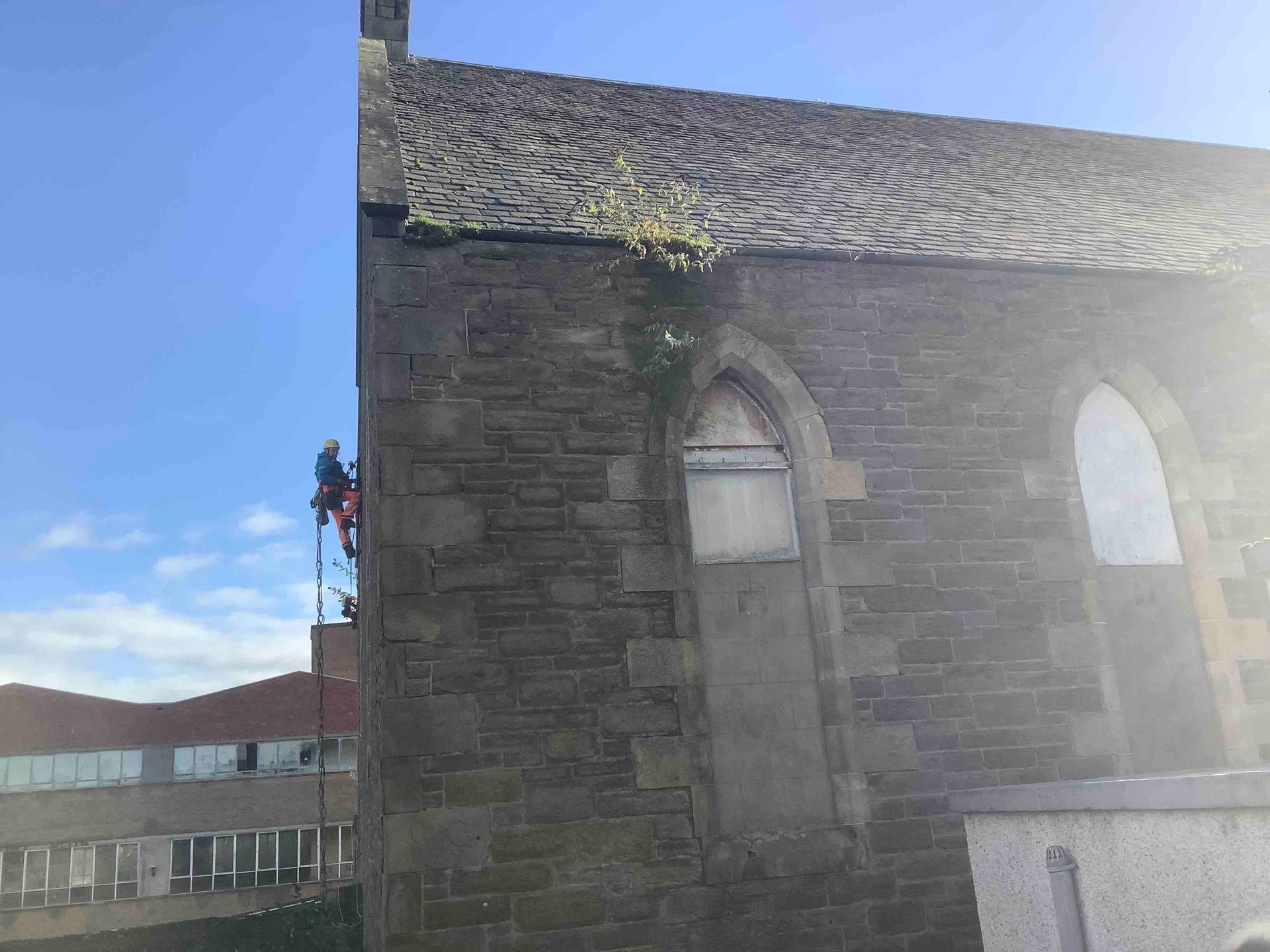